On this page
1. Blades |
2. Turbine towers |
3. Foundations |
4. Vessels |
5. Cables |
Together with our strategic partners, we’re taking the first steps towards net-zero wind farms. We’re the first in the industry to pursue low carbon solutions across all key offshore wind components. As the world’s largest offshore wind developer, we play a key role in incentivising investment in breakthrough low-carbon solutions and enabling our partners to test and scale them.
Offshore wind has played a central role in our decarbonisation journey so far and remains a key technology to curb the climate crisis. Even though carbon emissions from offshore wind are 99% lower than those from coal - per KWh of electricity generated, manufacturing, constructing, and operating an offshore wind farm still emits carbon. To meet our science-based net-zero goal, we need to eliminate these emissions.
Together with supply chain partners, we’re rolling out industry-leading solutions to decarbonise five key sources of greenhouse gas emissions from offshore wind – the first steps towards delivering the net-zero wind farms of tomorrow.
The largest sources of emissions in the lifecycle of an offshore wind farm come from producing components including blades, towers, foundations, and cables, along with powering the vessels used for transport, installation, operations, and site investigations. These are all emissions that need to be tackled as we continue to accelerate the build-out of offshore wind.
Taking action to decarbonise five key sources of greenhouse gas emissions from offshore wind
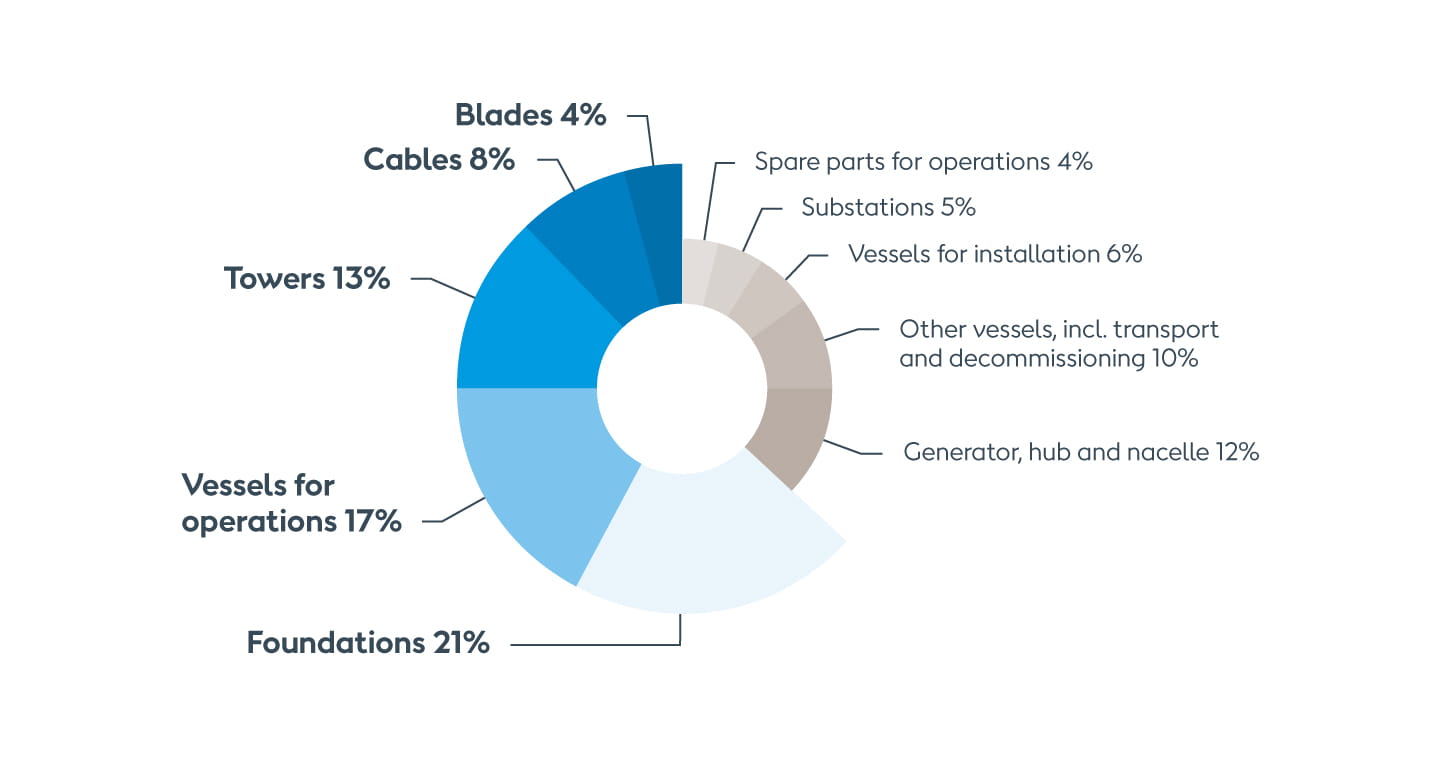
As one of the world’s largest renewable energy developers, we can act as a catalyst for change by building partnerships across the supply chain. Together we can create demand for low carbon solutions and drive the renewable energy sector to net-zero. Ørsted’s robust project pipeline creates a springboard to test our partners’ technological innovations and mature towards commercial scale, together. By committing to offtake low-carbon solutions, we give our partners the certainty they need to invest in them.
“
As the world’s largest offshore wind developer, we’re in a unique position to establish partnerships across the supply chain and enable investments in low-carbon technologies. By working together, we can lead our industry towards net-zero.
Virginie Van de Cotte
Chief Procurement Officer
Ørsted
Watch the video or read on to learn more about these decarbonisation solutions.
1. Blades made with recycled content with Vestas
Wind turbine blades are made of composite materials – typically a mix of glass fibres and either polyester or epoxy resins - which are difficult to recycle. This means that manufacturing them relies heavily on virgin resources, and that when it comes to disposal, there are limited alternatives to landfill. Considering the number of blades that are reaching end of life, this is the biggest circularity challenge facing our industry. In terms of emissions, blades account for around 5% of the total emissions from an offshore wind farm.
Current promising industry initiatives focus on changing blade design to make future blades recyclable. But our strategic supplier Vestas, together with academic and industrial partners, has come up with a new recycling solution that can break down composite materials in existing and future epoxy-based blades and use the recovered epoxy resin to manufacture new blades with recycled content. This innovation provides the solution for recycling the blades that are being decommissioned today and for the next many years to come, as well as the blades from the wind farms of the future. With this solution, we can start solving the industry’s circularity problem today.
We’re pleased to be entering into an industry-first partnership with Vestas to scale this technology and make sustainable procurement an integrated part of all commercial projects. When available, we will procure wind turbines made with recycled content in all future windfarms where we collaborate – a crucial step towards reducing our use of virgin resources.
2. Low emission steel turbine towers with Vestas
Wind turbine towers are made of steel, a highly carbon-intensive material. They account for around 15% of the total emissions from an offshore wind farm.
Together with Vestas, we are working to accelerate, scale-up, and drive demand for low emission steel for turbine towers. As part of our industry-first partnership mentioned above, we will procure a minimum of 25% low emission steel turbine towers for all future offshore wind projects where we are partnering. The low emission towers are made using scrap steel and a manufacturing process powered by renewable electricity.
This process has the potential to reduce emissions from steel plates used in turbine towers by up to 70%
3. Steel for foundations with lower carbon footprint with Dillinger
Offshore wind turbine foundations made from steel are the largest source of carbon emissions in the lifecycle of an offshore wind farm, accounting for around 20-30% of total emissions of a generic windfarm depending on foundations design.
We’re partnering with Dillinger, our long-term supplier of heavy plate steel, to develop for the first time ever steel with a lower carbon footprint for offshore wind turbine foundations.
These plates for foundations are to be produced in Dillinger’s new steel production, currently in planning: A direct reduced iron plant (DRI) that is to produce feedstock for their electric arc furnace (EAF). The DRI plant is planned to run hydrogen from renewable energies and natural gas, which will reduce the company’s emissions by up to 55%. The first steel with a low-carbon footprint at the Dillinger site is to be produced from 2027 onwards.
4. Crew transfer vessels powered by renewable energy
Fuels for operational logistics are the second largest source of greenhouse gas emissions across the lifecycle of an offshore wind farm, contributing around 15-20% of total emissions.
We will be deploying industry-leading pilot programmes using renewable electricity and e-methanol to power crew transfer vessels. The tests will take place at full-scale through our wind farm operations at Barrow and Lincs offshore wind farms in the UK.
Powering crew transfer vessels with electricity and e-methanol has the potential to reduce carbon emissions from operational logistics by up to 95 %.
5. Low-carbon copper cables with NKT
Offshore wind farms send their power ashore via export cables often composed with a copper core. The production and handling of these power cables and the extraction and processing of metals are responsible for around 10% of an offshore wind farm’s lifecycle emissions.
We’re partnering with power cable supplier NKT to ensure that all copper export cables at the Hornsea 3 offshore wind farm in the UK will be low carbon.
NKT has succeeded in producing low carbon cables by deploying renewable electricity throughout various stages of the value chain. Using vehicles and smelters powered by fossil-free electricity, electric train transport, and efficient manufacturing processes, they have been able to reduce the carbon footprint of the high-voltage power cables by up to 49%.